Simulation
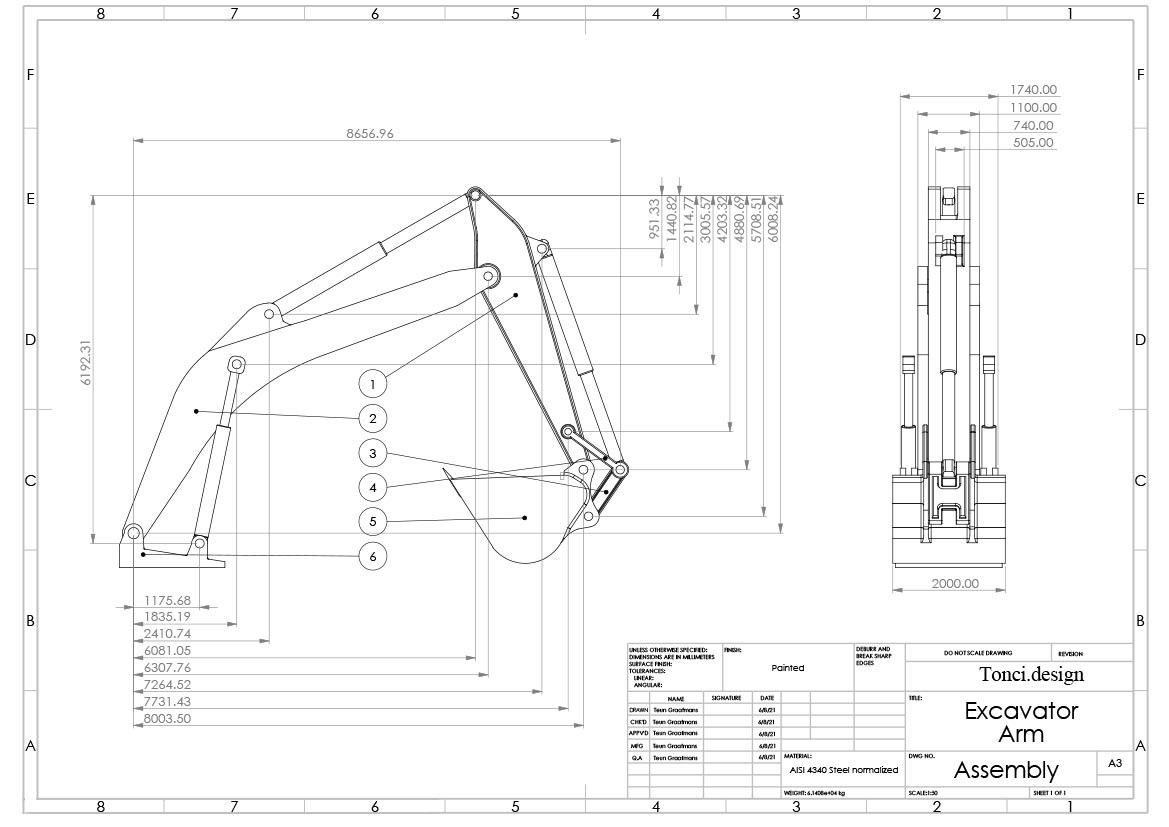
Virtual verification
Solo project
Briefing
I had to verify a CAD model using Solidworks Simulations. The calculation must contain at least five parts. Afterwards, two parts needed to be improved. One should be improved in shape and one needs to be improved in material.
Intro
I chose a hydraulic excavator arm from grabcad for the assignment. The arm is used for heavy industrial purposes so the load on the model is fairly heavy.
Material & Load
Material
The material for industrial machinery is usually something like AISI 4340 Steel normalized. This material has been applied to all the parts in the assembly.
Load
The volume of the bucket is calculated by Solidworks and is 3839046910.75mm3 which is 3.83904691075m3. I took the density of wet sand as the heaviest load. The density of wet sand is 2 039kg/m3. This results in a load of 3.83904691075*2039*10=78,3kN. To take the dynamic use into account, I've multiplied this by 1.3 which results in 101.8kn.
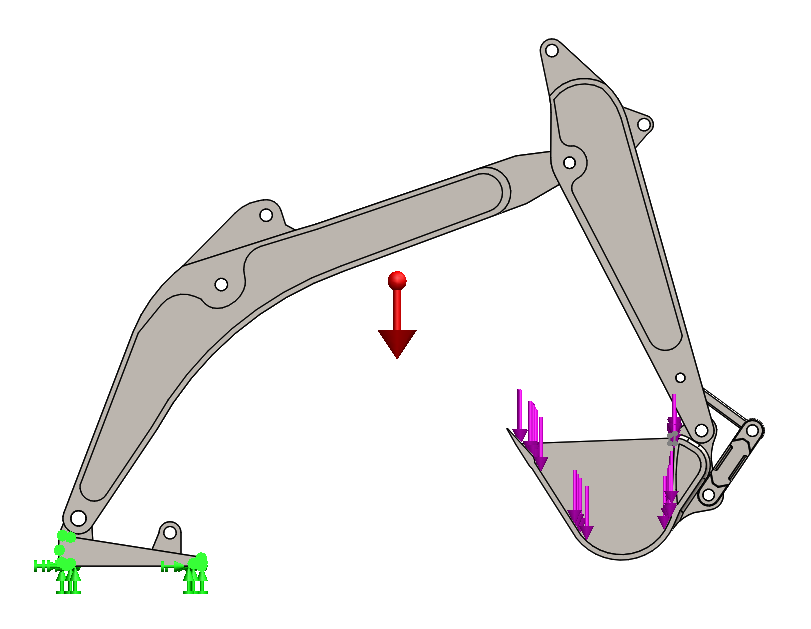
Fixtures
Fixed geometry
There are no clear mounting points on part 6 so I locked it in place with a fixed geometry.
Symmetry fixture
To reduce the calculation time and save computational resources, I've split the model in half and applied a symmetry fixture.
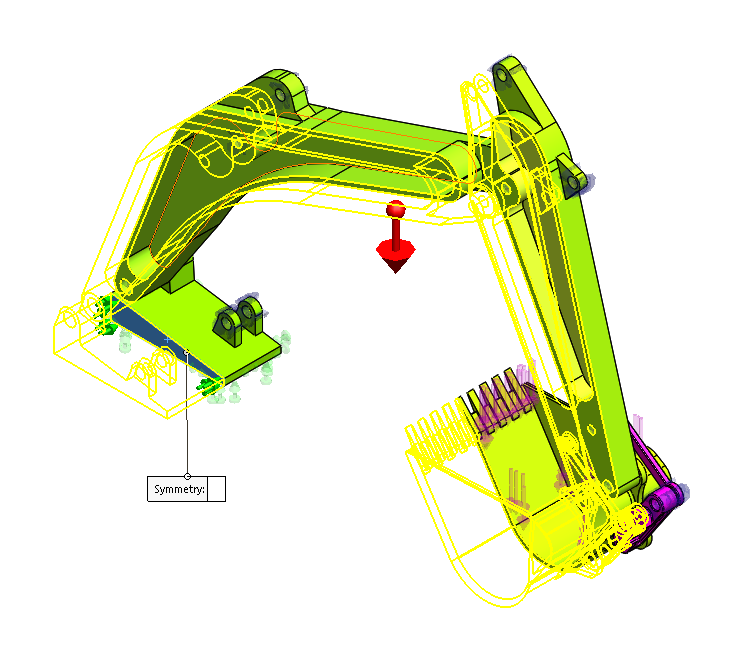
Connectors
Rigid connectors
Again for reduced calculation time and computational resources, I've replaced the hydraulic cylinders with rigid connectors. These will pass on the resultant forces but won't be part of the simulation.
Pin connectors
I've calculated the tensile stress area for every individual pin.
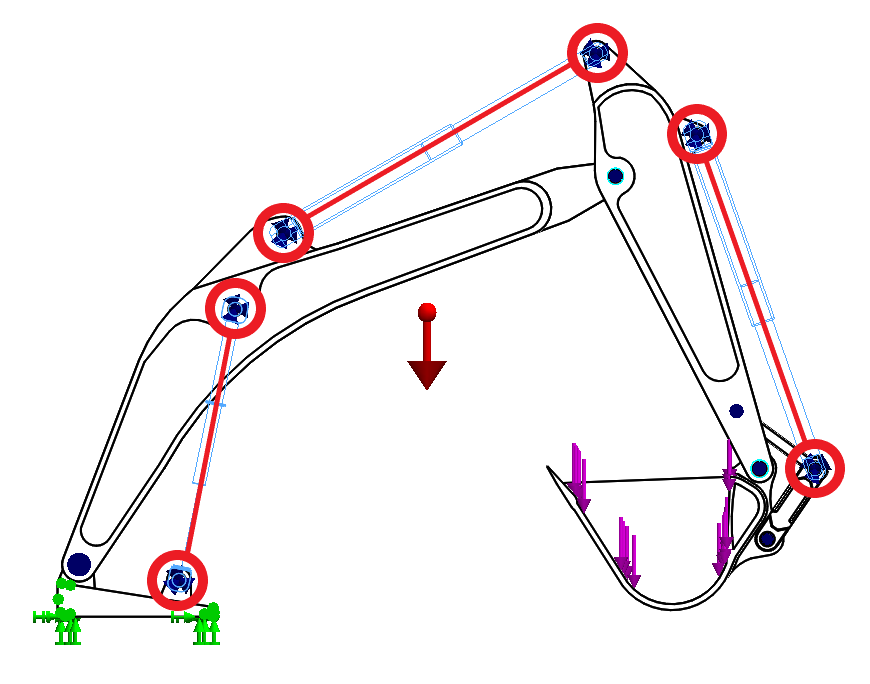
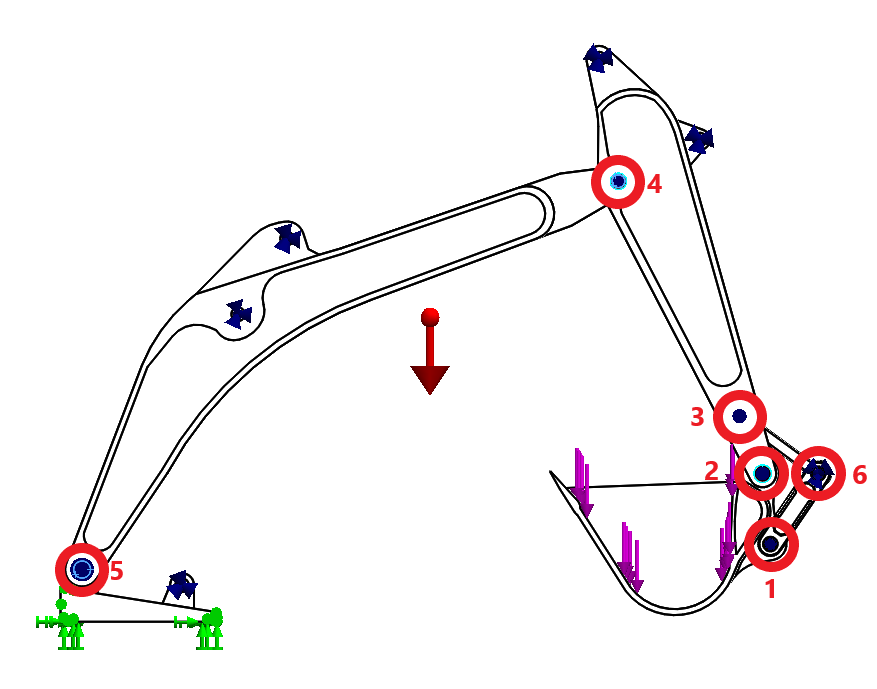
Mesh
I started with a quick simulation, to locate the high stress hot spots. Mesh control will be applied at those hot spots. I've used two ways of applying mesh control: on part level and on surface level.
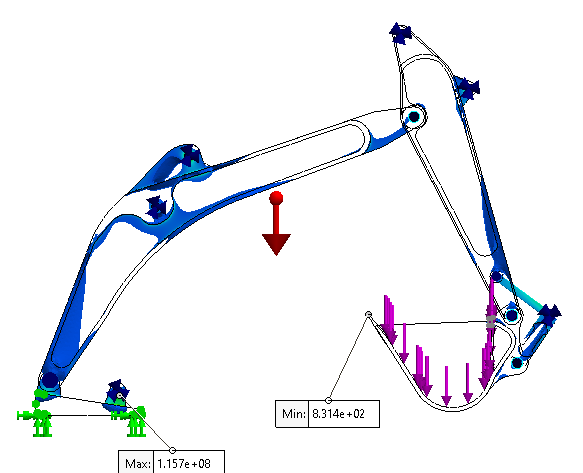
Surface improvements
A few of the sharp corners were fileted to avoid infinite stress. Some volumes were not well constructed and gave me an uneven mesh. I remodeled these to get a better distributed mesh.
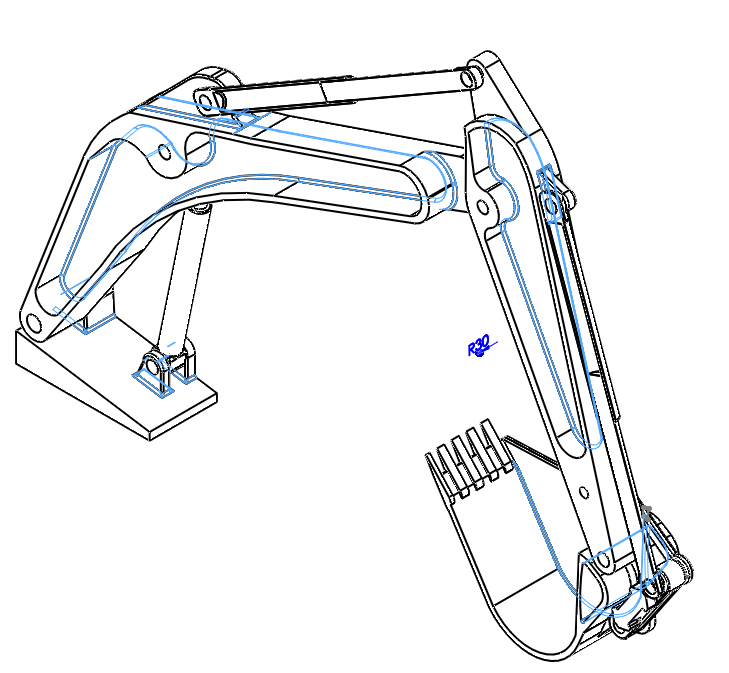
Calculation 1
From the results, I can conclude that the overall model is too strong. The most notable parts are part 1 and 5. I decided to improve part 1 on shape and part 5 on material.
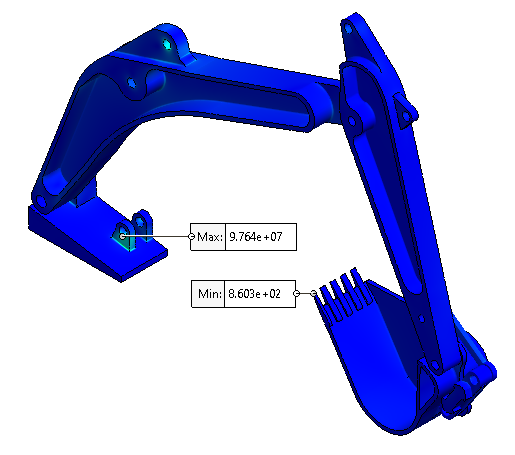
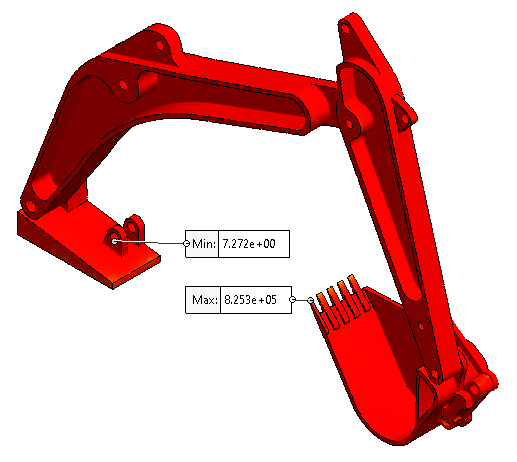
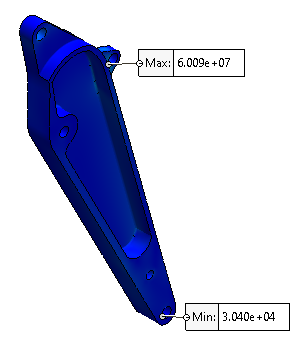
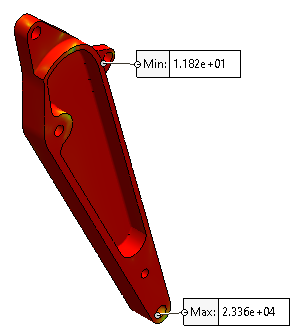
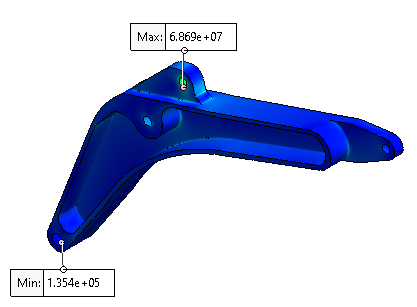
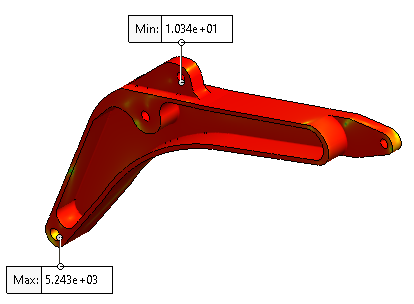
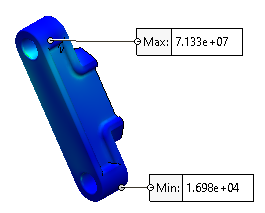
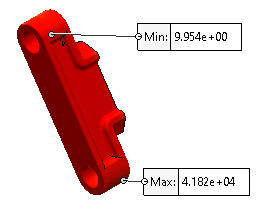
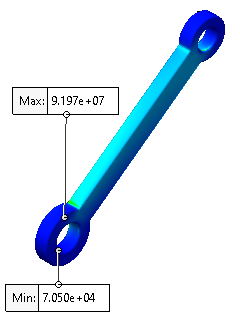
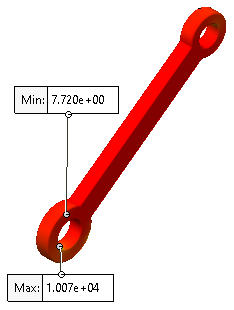
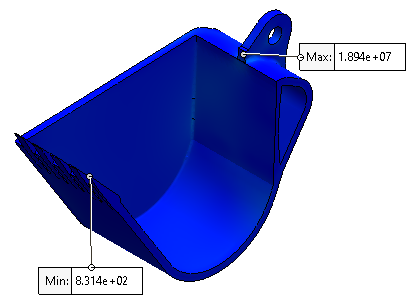
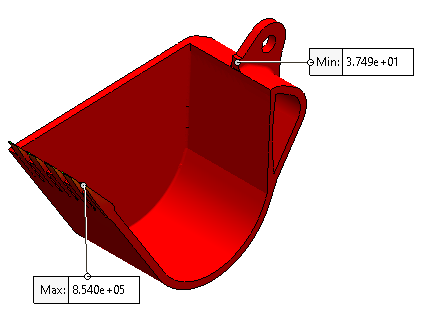
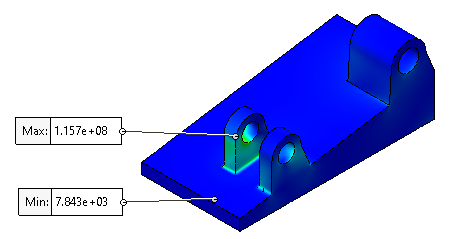
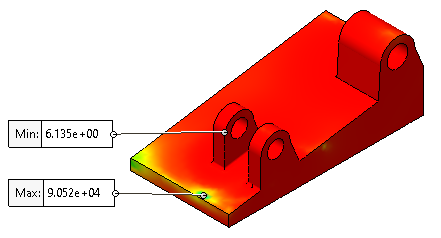
Material improvement
Part 5 is changed from AISI 4340 Steel normalized to a material with a lower yield strength. The part is isolated for the purpose of saving time and computational resources. The first calculation has been redone with the original material with a yield strength of 710 N/mm2 and a tensile strength of 1110 N/mm2. The result is a maximum Von mise stress of 1.827e+07 which results in a factor of safety of 3.886e+01. This is almost 39 times stronger than it needs to be.
The original material was swapped out with AISI 316 annealed stainless steel. This material has a much lower yield strength at 137.9 N/mm2 and a tensile strength of 550 N/mm2.
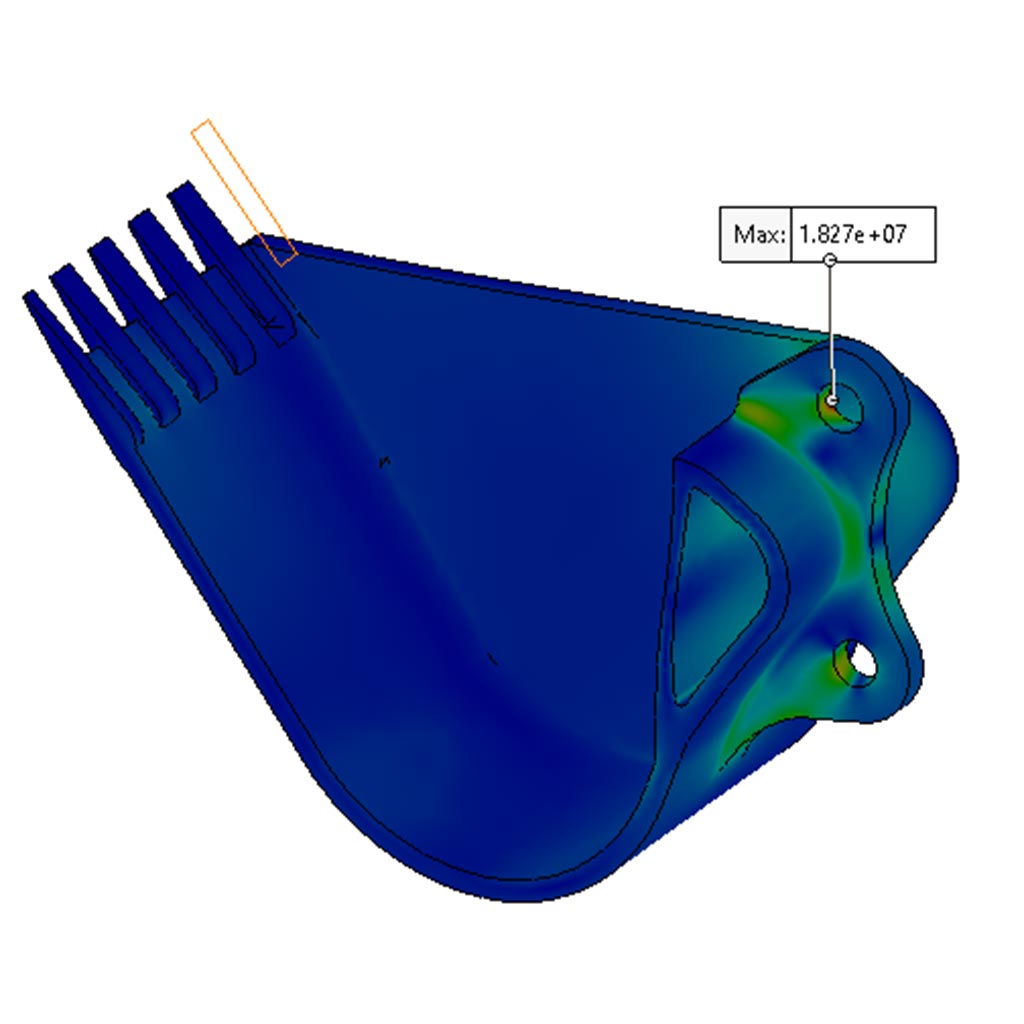
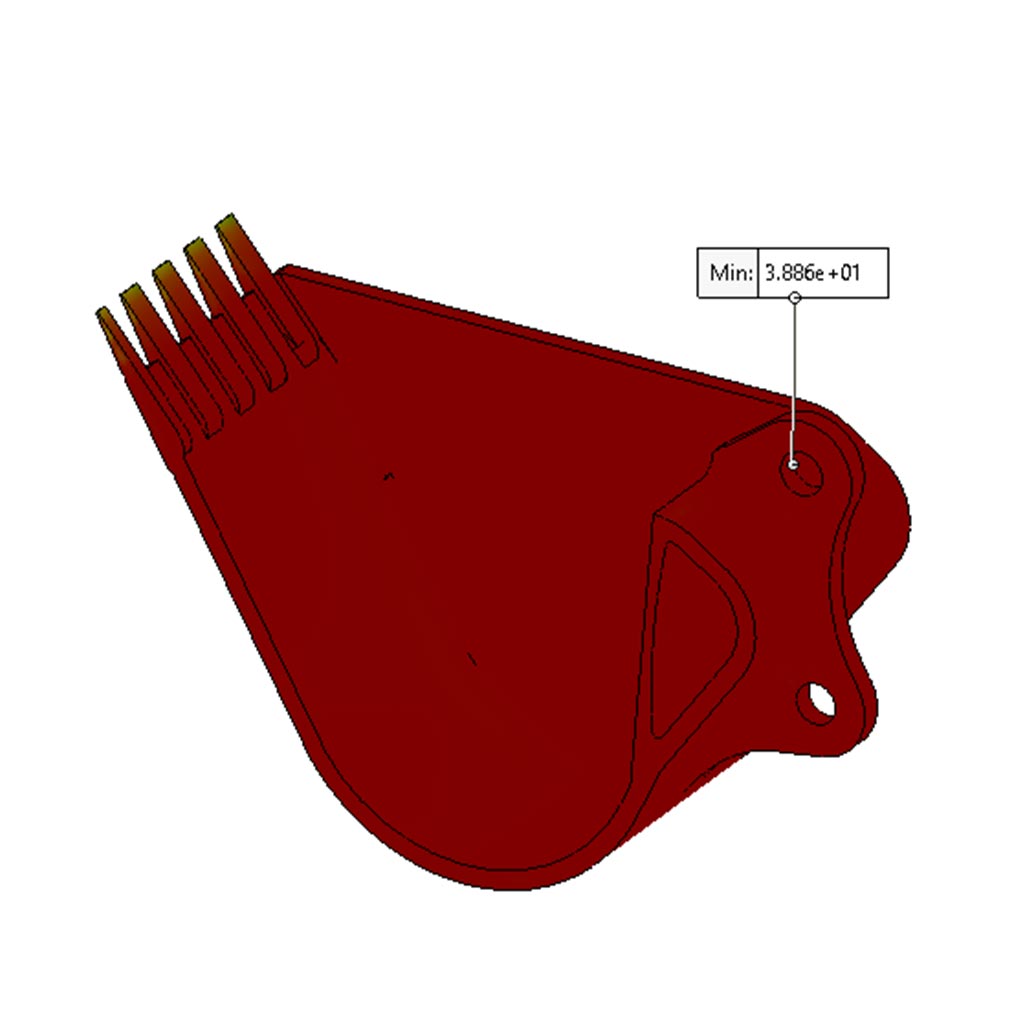
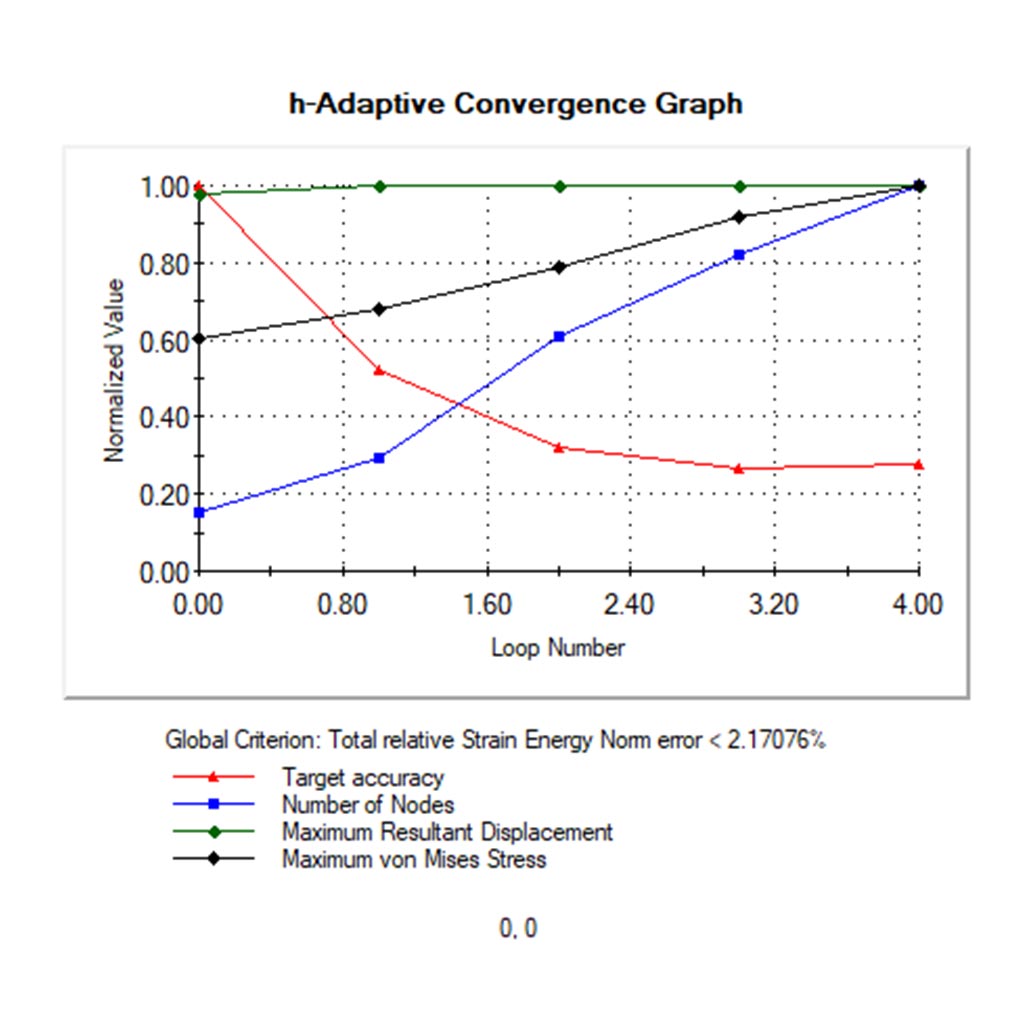
Calculation 2
The calculation after the change in material shows almost the same Von Mise stress, which is a sign of a relevant result. Looking at the convergence graph we can confirm this result as valid. The factor of safety changed from 38.86 to 7.477. This is still too strong for this part. Altering the material alone is not enough to get this part FOS to the desired 2-3. An additional improvement on shape is needed to get to the sweet spot between cost and strength.
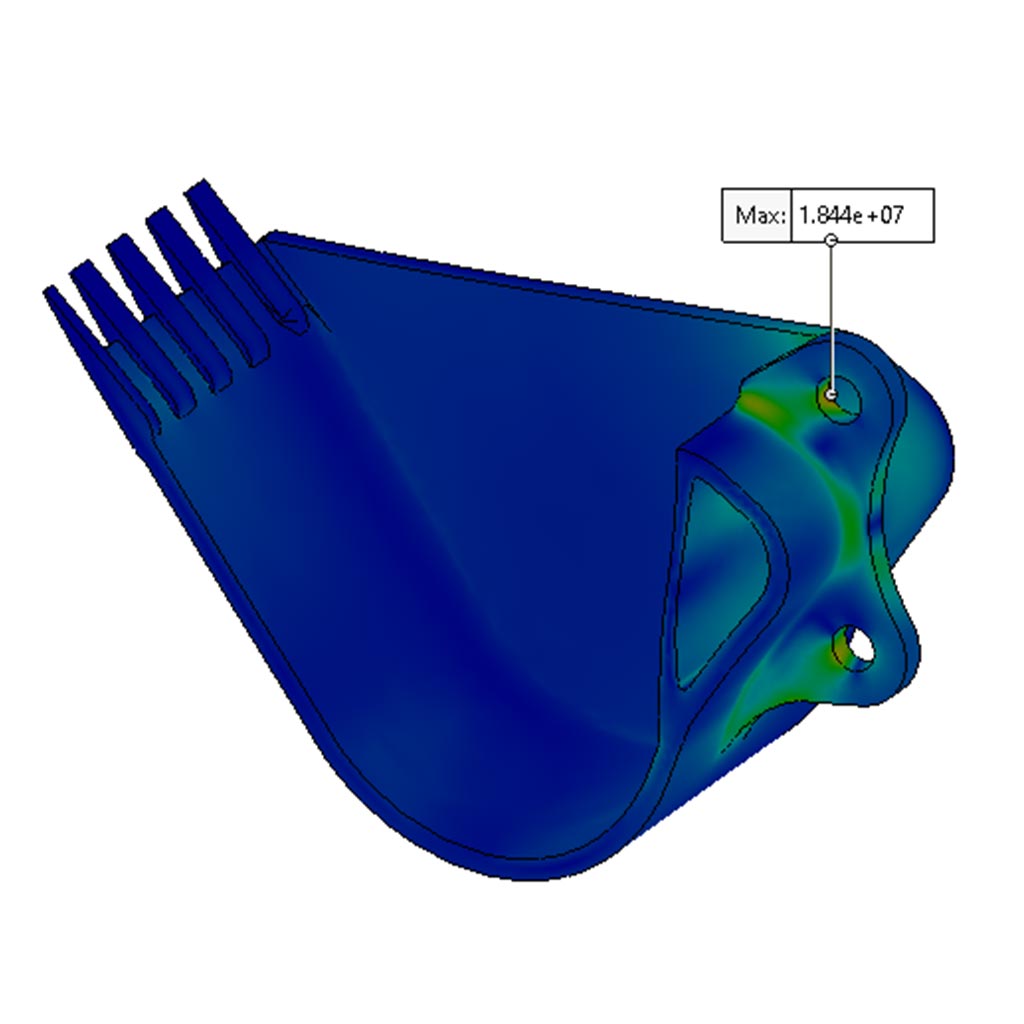
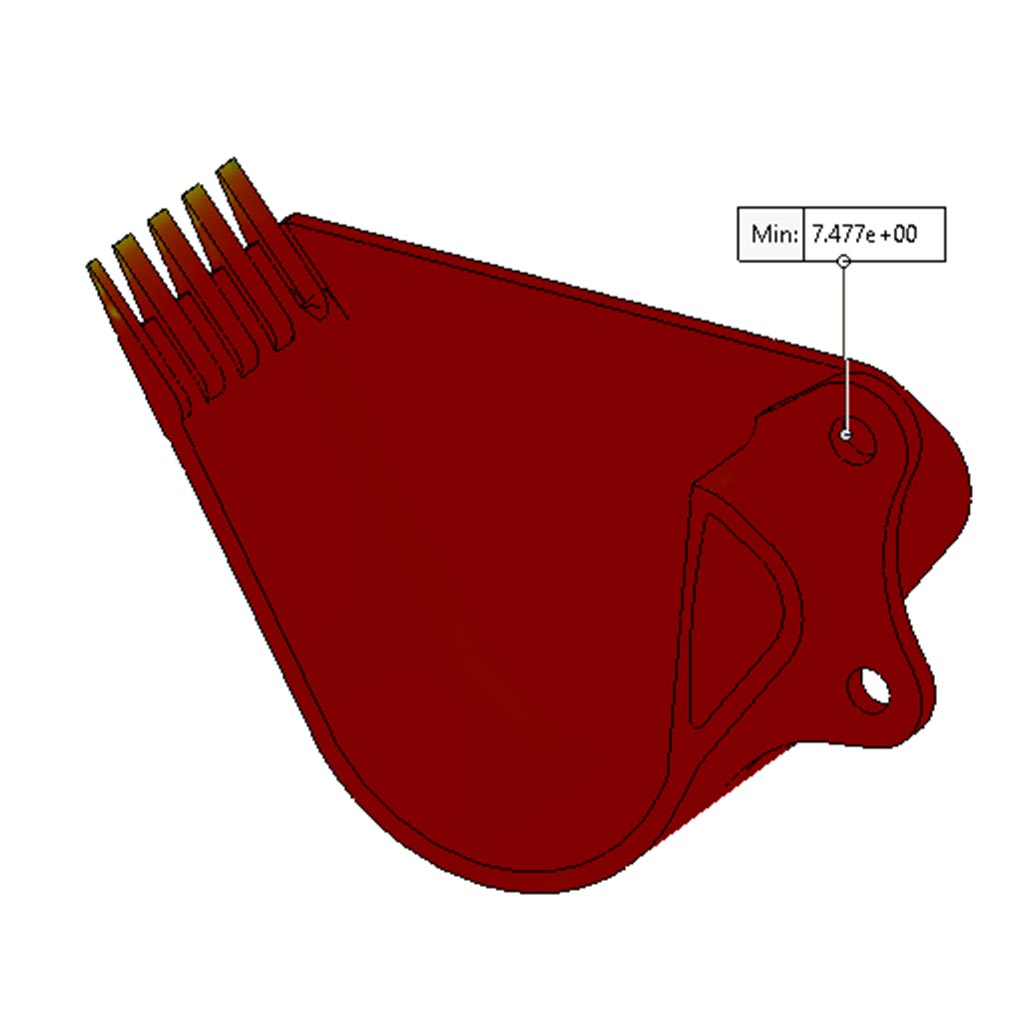
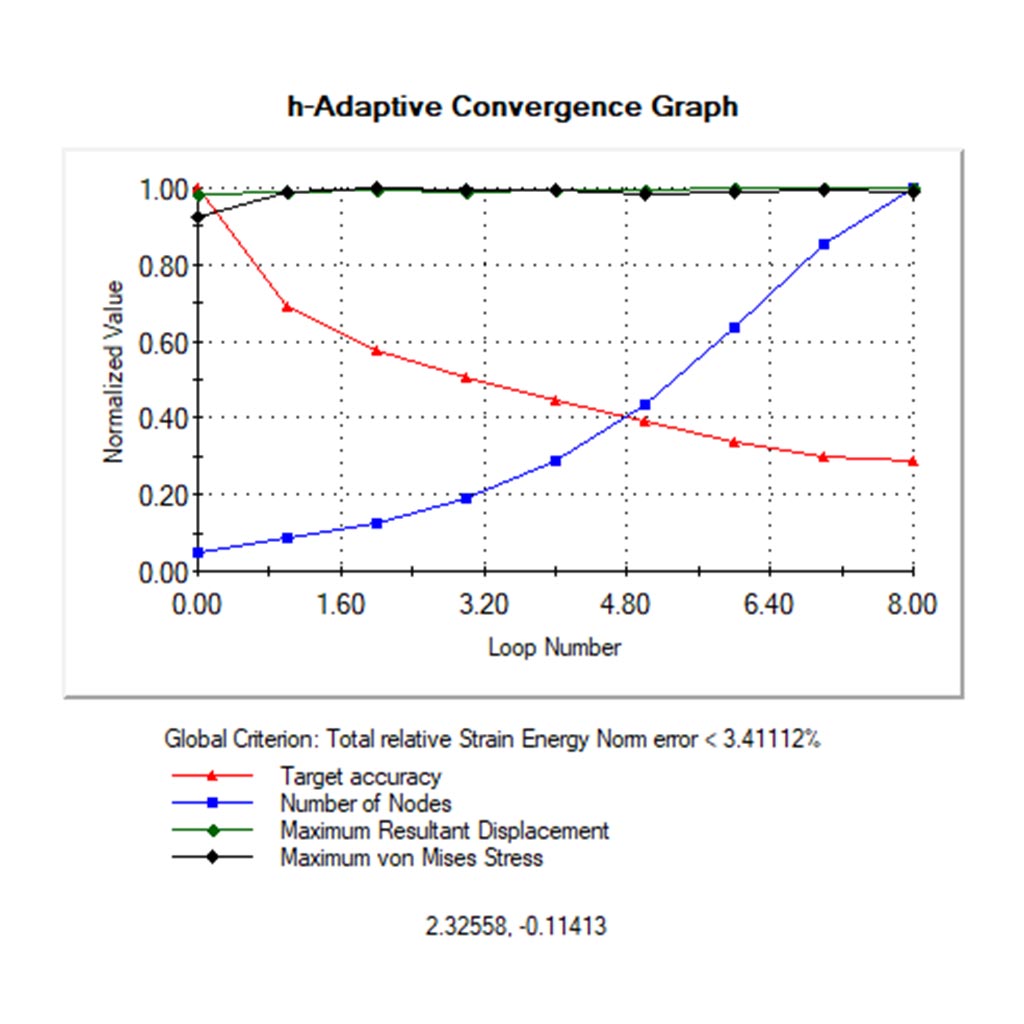
Shape improvement
The stress in part 1 is not well distributed to the whole body so the shape of this part needs to change. The shell contains too much material so thickness needs to be reduced. A 70% reduction in thickness is applied which means it goes from 100mm to 30mm. The back panel receives most of the stress so it needs to be a bit stronger. This is changed from 100mm to 40mm.
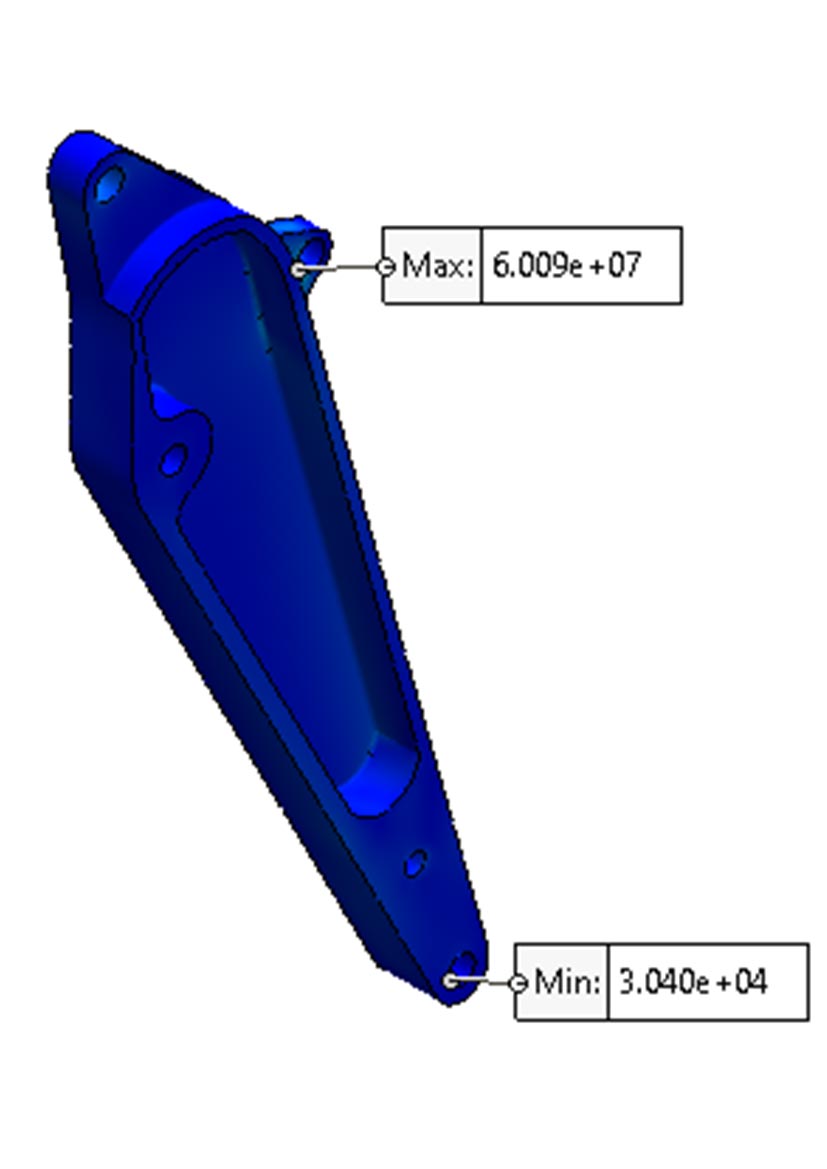
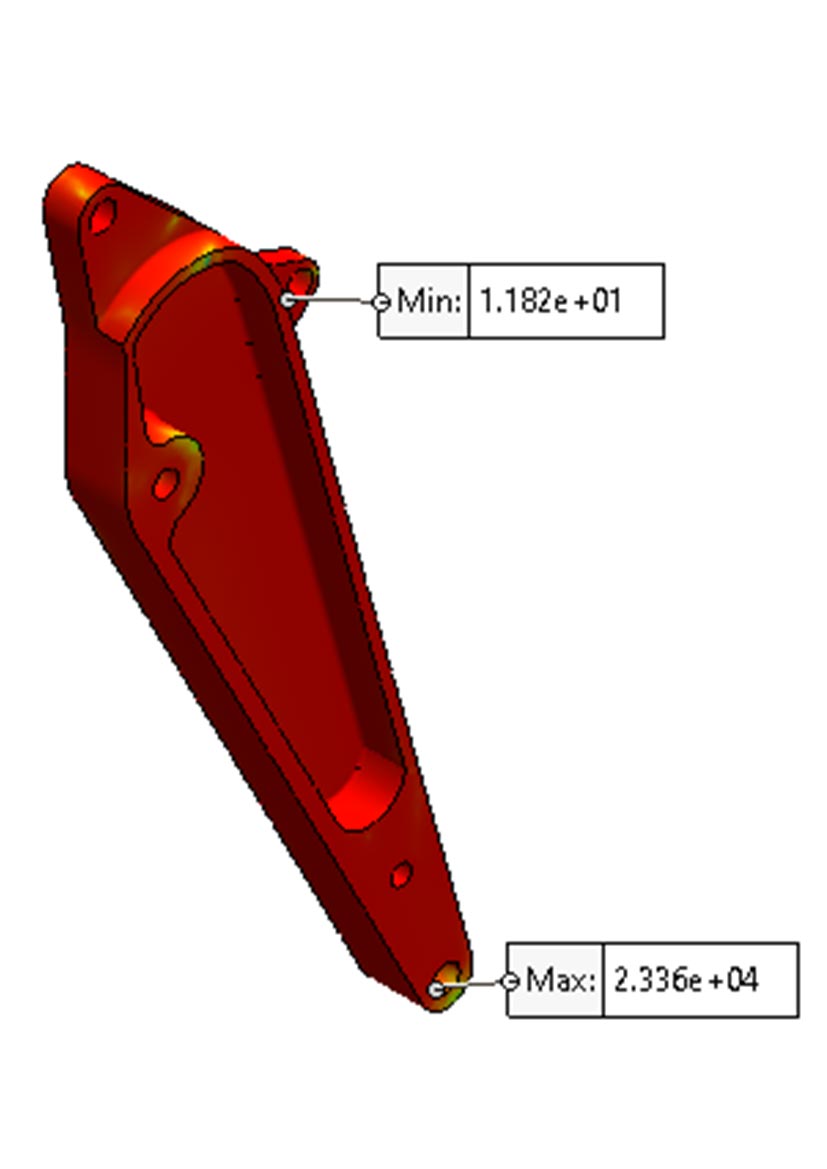
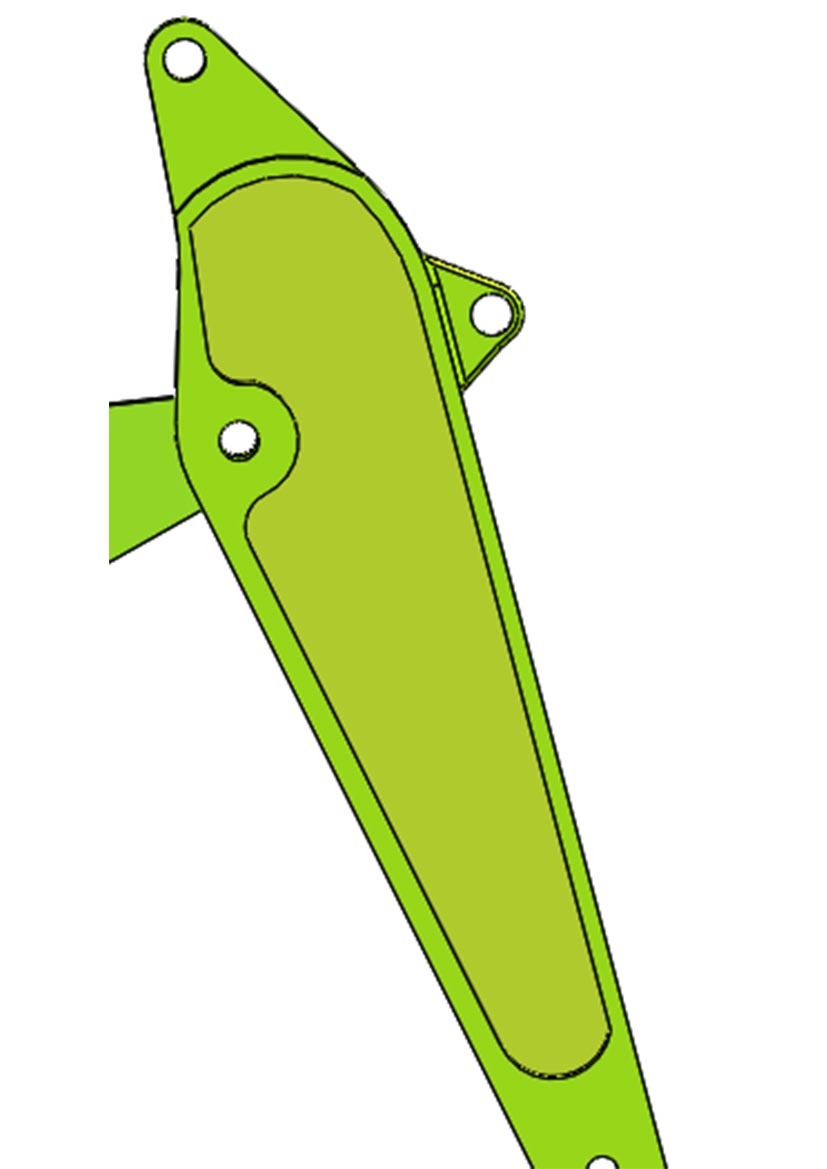
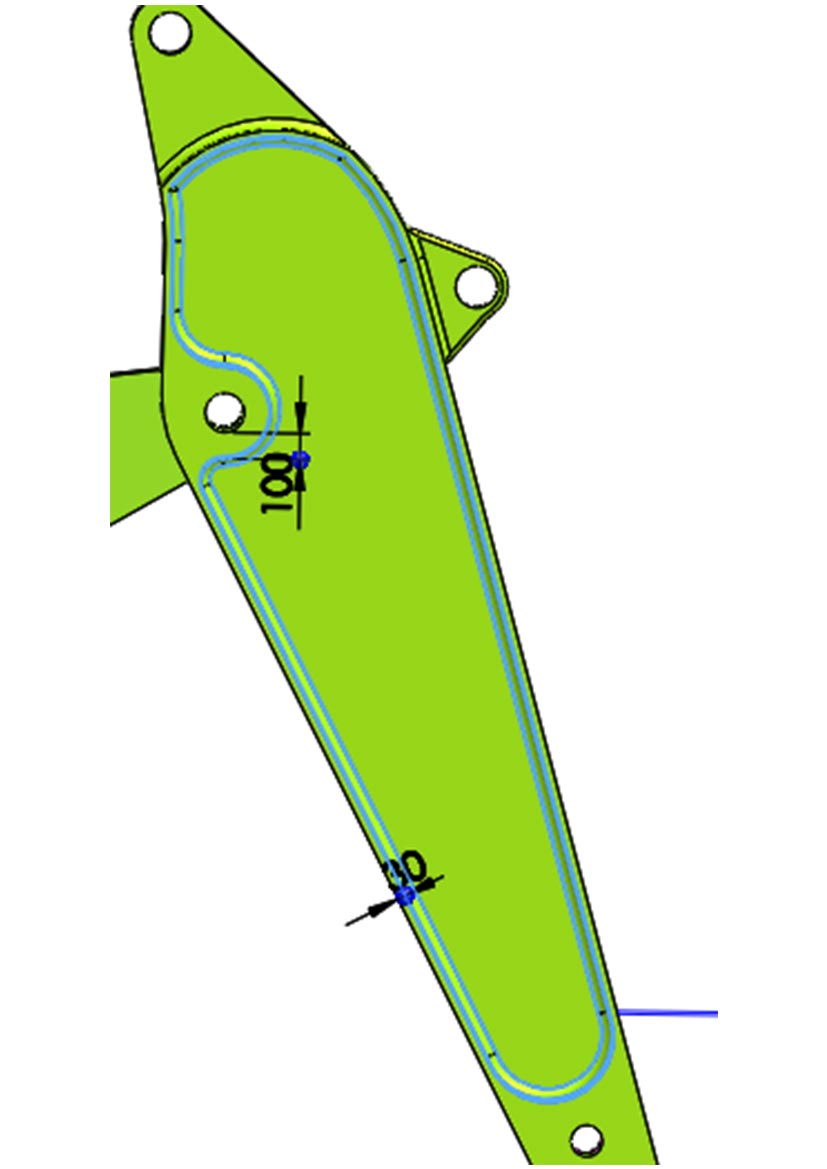
Calculation 3
The factor of safety has not changed that much but the stress is much better distributed over the whole part. The stress is penetrating a lot deeper in the material, shown by the iso clipping heat maps. The iso clipping is set to 7.0e+06 N/mm2.
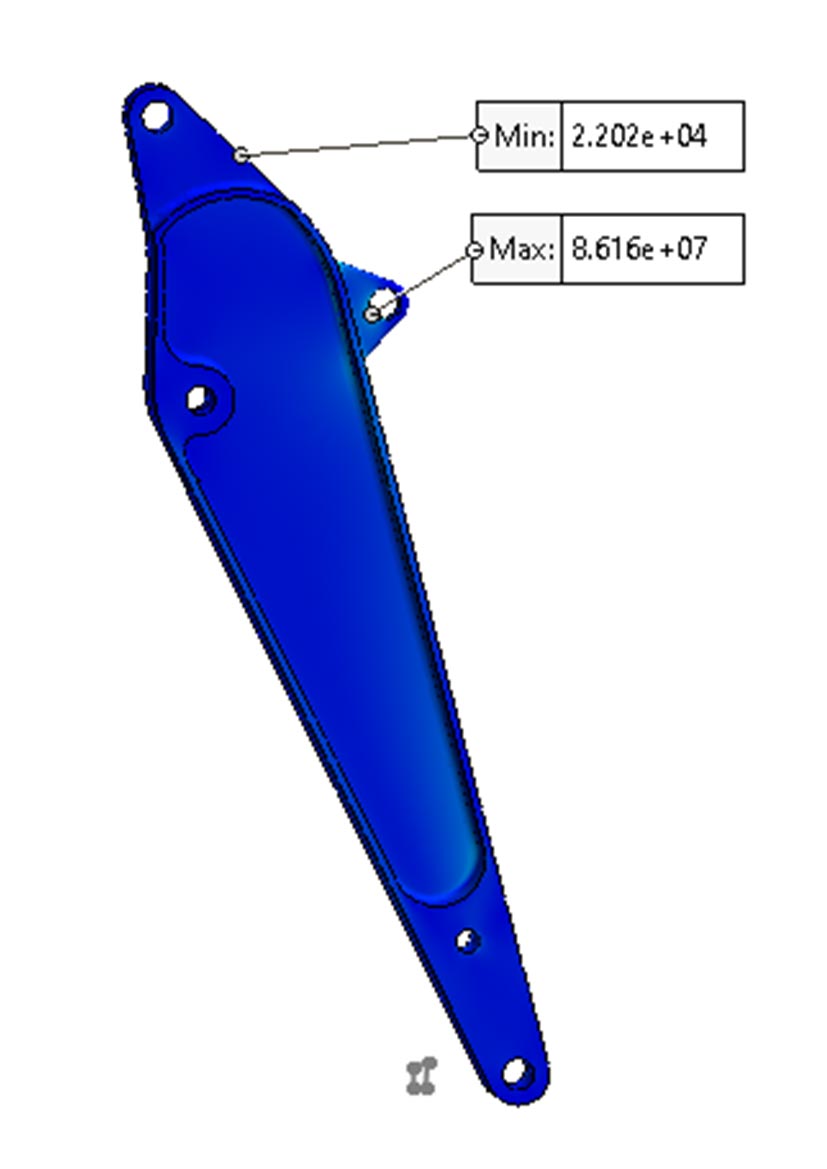
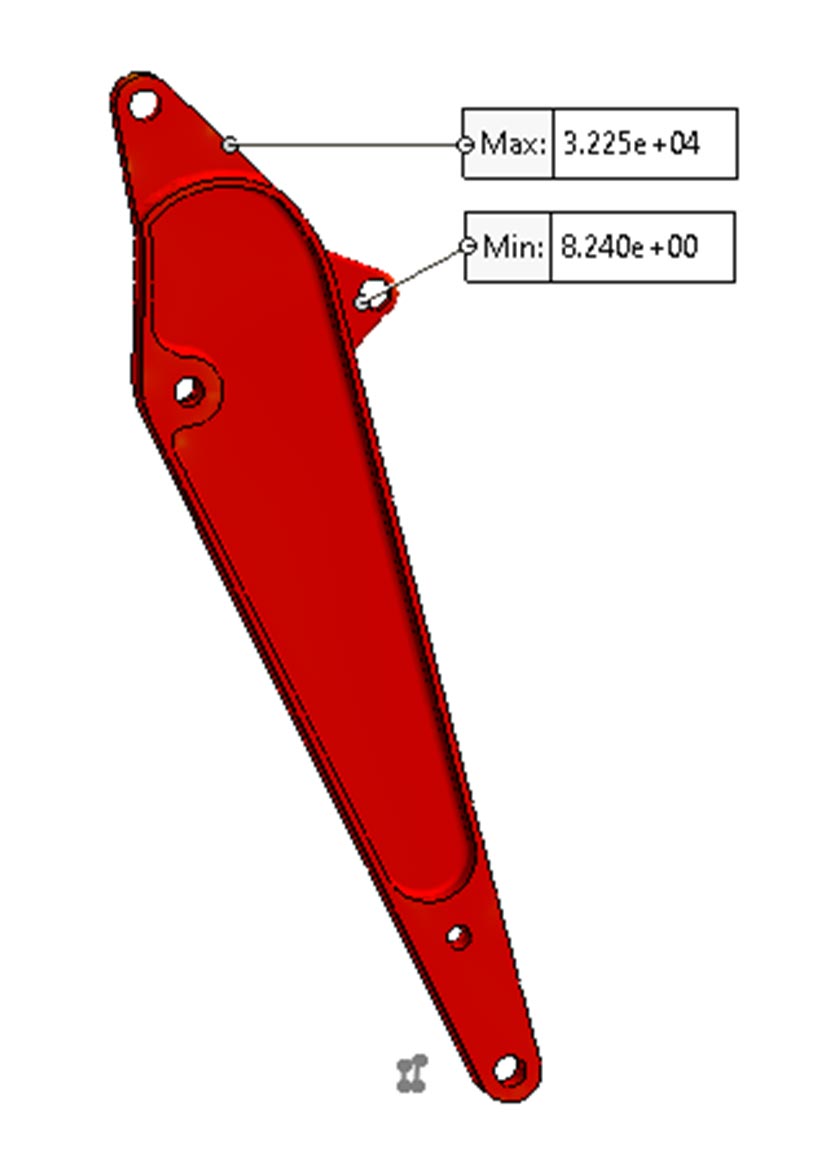
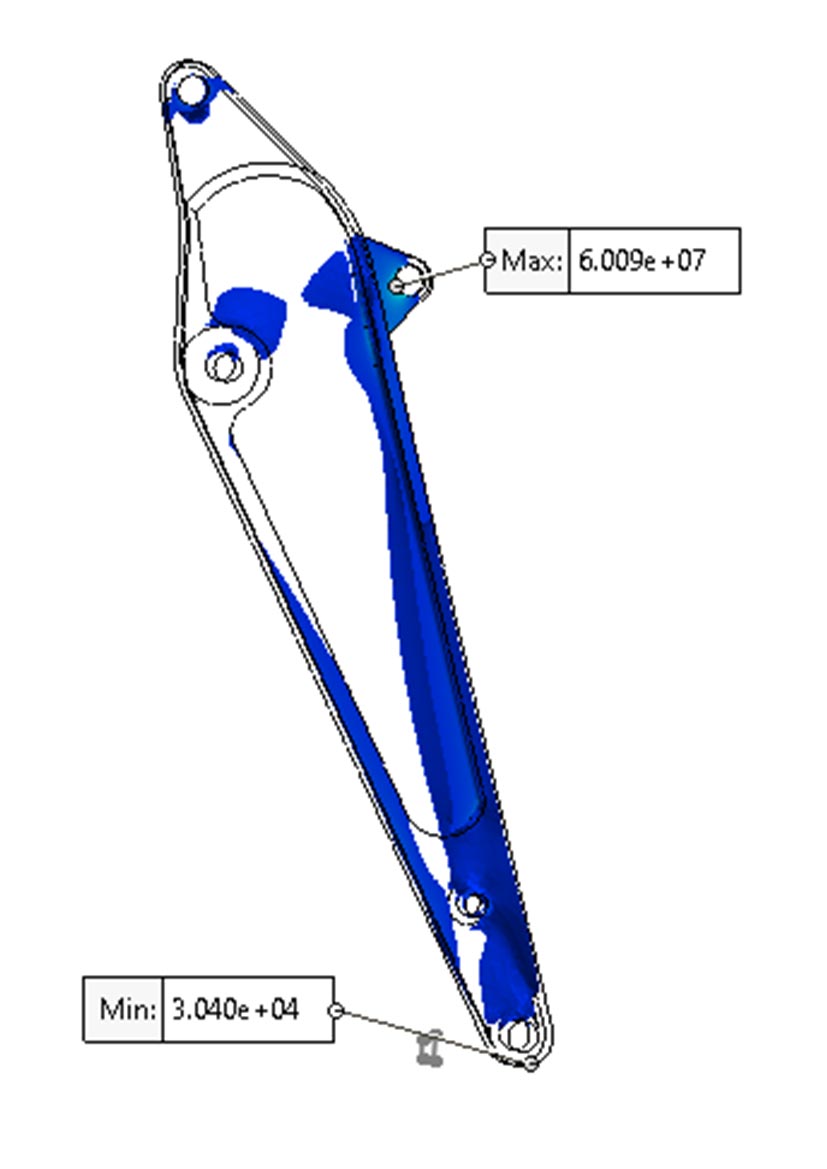
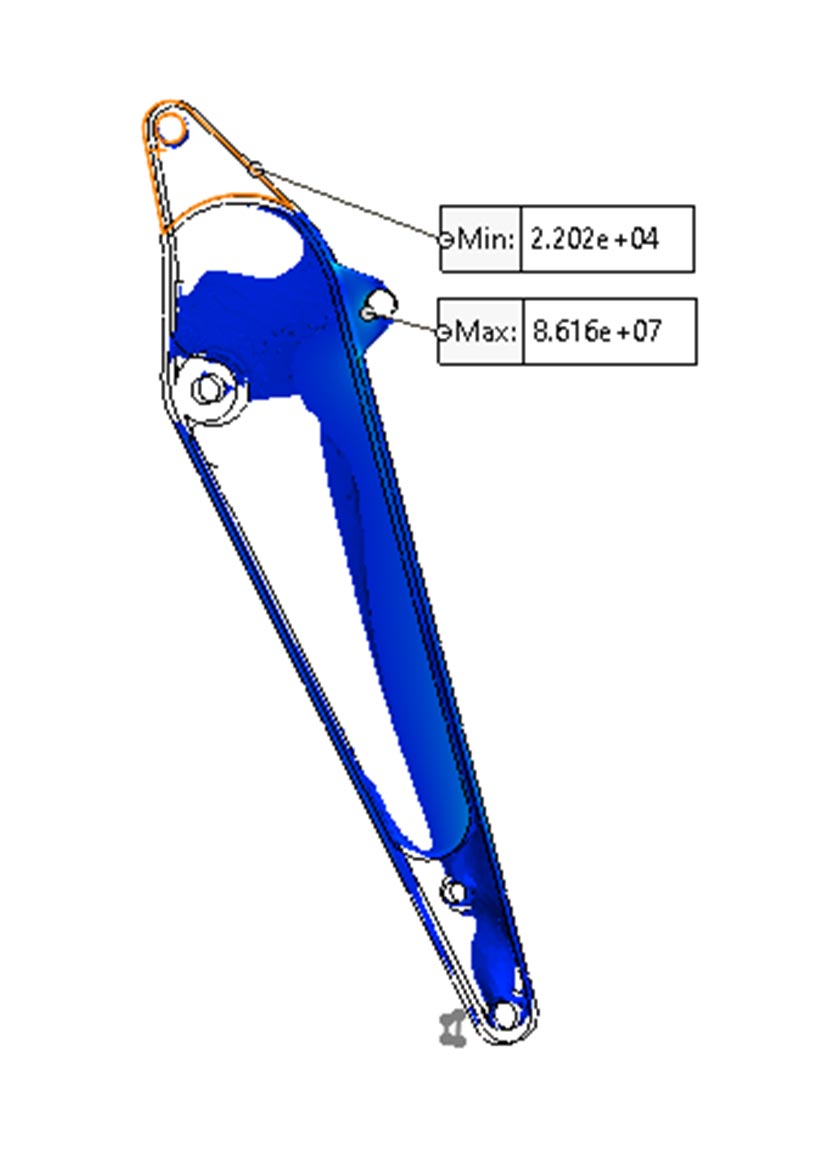
Conclusion
The original model had a lot of problems at the start. Besides being much too strong, it also lacks in terms of quality surface to surface transitions. This makes some simulations unsolvable because there will be values of zero which result in infinite stress. The improved parts still have room for more improvement but it is enough for the sake of this assignment.